Inspections
Inspections
Inspections
Inspections Overview
The ASAM software allows inspection results to be stored and retrieved easily and effectively. All too often data is stored in various IT systems, but cannot be accessed easily by the personnel requiring it.
The basic OH&S statement relating to Confined Space Access is ‘don’t go in if you cannot get out” This should also apply to data entry – “don’t enter it in if you cannot retrieve it when required”
There is an appropriate statement that applies to most industries – “if it hasn’t been measured, then it cannot be managed”.
This section lists common areas that need to be inspected and reported upon on a regular basis, using skilled, ‘fit for purpose’ personnel.
Each category begins with an overview explanation and appropriate images showing some of the most common issues identified to date.
The ASAM software allows inspection results to be stored and retrieved easily and effectively. All too often data is stored in various IT systems, but cannot be accessed easily by the personnel requiring it.
The basic OH&S statement relating to Confined Space Access is ‘don’t go in if you cannot get out” This should also apply to data entry – “don’t enter it in if you cannot retrieve it when required”
There is an appropriate statement that applies to most industries – “if it hasn’t been measured, then it cannot be managed”.
This section lists common areas that need to be inspected and reported upon on a regular basis, using skilled, ‘fit for purpose’ personnel.
Each category begins with an overview explanation and appropriate images showing some of the most common issues identified to date.
Inspections
Inspections Overview
The ASAM software allows inspection results to be stored and retrieved easily and effectively. All too often data is stored in various IT systems, but cannot be accessed easily by the personnel requiring it.
The basic OH&S statement relating to Confined Space Access is ‘don’t go in if you cannot get out” This should also apply to data entry – “don’t enter it in if you cannot retrieve it when required”
There is an appropriate statement that applies to most industries – “if it hasn’t been measured, then it cannot be managed”.
This section lists common areas that need to be inspected and reported upon on a regular basis, using skilled, ‘fit for purpose’ personnel.
Each category begins with an overview explanation and appropriate images showing some of the most common issues identified to date.
Site security is one of the first controlling points for protecting water quality.
Sites left unattended can become attractive to vandals and other unauthorised persons, thus increasing the risk of site damage, field staff safety and contamination exposure points.
Regular site inspections are necessary and the installation of remote security cameras will assist in deterring unauthorised access to the tank site.
Ensuring existing security compounds are not downgraded by other works such as installation of electrical cabinets close to the ladder compound, which create a step/pathway to climb past the compound.
Removing debris from around the site, such as lengths of timber, old pallets and any materials that can be used to create a bypass system to the ladder compound.
Trimming back overhanging trees and vegetation that allow access over or through the security compound fence.
OH&S is an important part of the workplace and there has been a concerted effort in training and PPE to reduce risks to personnel.
There is still a long way to go however in designing out the ‘not so obvious’ risks present in our daily workplaces.
Outdated Australian Standards still ask for features that have proved to be dangerous in certain situations, such as cages and platforms on ladders fitted into confined spaces.
Specific Australian Standards do not always take into account other AS regulations with a similar agenda, but requiring different outcomes.
A balance must be achieved by consulting all the relevant AS and then deciding which is the most appropriate design to make the outcomes ‘fit for purpose’.
An often heard statement is “Our water meets all standards and requirements as it leaves the Treatment plant”.
While that is probably true, a lot can and does happen downstream of the ‘conforming’ Treatment plant.
Water travels in pipework systems that are many years old, is stored in tanks that are poorly sealed and maintained, and is often ‘aged’ and past its quality parameters before it arrives to the consumer.
A better understanding of what occurs along the way and how the system can be upgraded and improved is a basic requirement for any ‘food grade’ product.
Disinfection levels are often compromised by contaminants found within the distribution and storage systems.
- Deliberate contamination caused by vandalism activities when security is poor
- Natural contamination from vermin entry or bird faecal build-up around unsecured or unsealed fixtures such as hatches, ventilation and roof fittings
- Structural contamination from unsuitable construction materials causing corrosion or poor water movement within the storage
There are the obvious and not so obvious things when it comes to structural issues.
All materials used in water transportation or storage need to be ‘fit for purpose’. What is suitable in a normal factory or building situation is often not suitable in a hot, humid and often chemical infused environment.
Many water assets are at least half way through their design lives, so concrete spalling from corroding reinforcement bars and chloride impacts from the surrounding environment are to be expected.
Steel structures need to have effective protective coatings in place to avoid destructive corrosion impacts.
Jointing materials and pipework have shorter design lives than the main asset shell, so mid-life renovations will be required to avoid leakage failures.
Testing the external surfaces of a concrete water storage tank will allow renovation decisions to be made in time, before more serious problems develop and require expensive remediation’s to be carried out.
Concrete structures deteriorate over time, due to several common factors.
- Design issues, poor workmanship and inferior/unsuitable materials used during the construction phase
- Carbonation of the external concrete surfaces, which reduces the alkalinity and then affects the ability of the reinforcing steel to remain passive
- Chloride uptake of the concrete, caused by either backfilling with unsuitable materials or the initial concrete mix having a high chloride content
- Shallow reinforcing steel cover, whereby the above carbonation and chloride issues will affect the structural strength of the concrete quicker than anticipated.
- Insufficient amounts of reinforcing steel, causing Thermal Cracking due to heating on the outside and cool water on the inside
Scroll through the images above ↑
Site security is one of the first controlling points for protecting water quality.
Sites left unattended can become attractive to vandals and other unauthorised persons, thus increasing the risk of site damage, field staff safety and contamination exposure points.
Regular site inspections are necessary and the installation of remote security cameras will assist in deterring unauthorised access to the tank site.
Ensuring existing security compounds are not downgraded by other works such as installation of electrical cabinets close to the ladder compound, which create a step/pathway to climb past the compound.
Removing debris from around the site, such as lengths of timber, old pallets and any materials that can be used to create a bypass system to the ladder compound.
Trimming back overhanging trees and vegetation that allow access over or through the security compound fence.
Scroll through the images above ↑
OH&S is an important part of the workplace and there has been a concerted effort in training and PPE to reduce risks to personnel.
There is still a long way to go however in designing out the ‘not so obvious’ risks present in our daily workplaces.
Outdated Australian Standards still ask for features that have proved to be dangerous in certain situations, such as cages and platforms on ladders fitted into confined spaces.
Specific Australian Standards do not always take into account other AS regulations with a similar agenda, but requiring different outcomes.
A balance must be achieved by consulting all the relevant AS and then deciding which is the most appropriate design to make the outcomes ‘fit for purpose’.
Scroll through the images above ↑
An often heard statement is “Our water meets all standards and requirements as it leaves the Treatment plant”.
While that is probably true, a lot can and does happen downstream of the ‘conforming’ Treatment plant.
Water travels in pipework systems that are many years old, is stored in tanks that are poorly sealed and maintained, and is often ‘aged’ and past its quality parameters before it arrives to the consumer.
A better understanding of what occurs along the way and how the system can be upgraded and improved is a basic requirement for any ‘food grade’ product.
Disinfection levels are often compromised by contaminants found within the distribution and storage systems.
- Deliberate contamination caused by vandalism activities when security is poor
- Natural contamination from vermin entry or bird faecal build-up around unsecured or unsealed fixtures such as hatches, ventilation and roof fittings
- Structural contamination from unsuitable construction materials causing corrosion or poor water movement within the storage
Scroll through the images above ↑
There are the obvious and not so obvious things when it comes to structural issues.
All materials used in water transportation or storage need to be ‘fit for purpose’. What is suitable in a normal factory or building situation is often not suitable in a hot, humid and often chemical infused environment.
Many water assets are at least half way through their design lives, so concrete spalling from corroding reinforcement bars and chloride impacts from the surrounding environment are to be expected.
Steel structures need to have effective protective coatings in place to avoid destructive corrosion impacts.
Jointing materials and pipework have shorter design lives than the main asset shell, so mid-life renovations will be required to avoid leakage failures.
Scroll through the images above ↑
Testing the external surfaces of a concrete water storage tank will allow renovation decisions to be made in time, before more serious problems develop and require expensive remediation’s to be carried out.
Concrete structures deteriorate over time, due to several common factors.
- Design issues, poor workmanship and inferior/unsuitable materials used during the construction phase
- Carbonation of the external concrete surfaces, which reduces the alkalinity and then affects the ability of the reinforcing steel to remain passive
- Chloride uptake of the concrete, caused by either backfilling with unsuitable materials or the initial concrete mix having a high chloride content
- Shallow reinforcing steel cover, whereby the above carbonation and chloride issues will affect the structural strength of the concrete quicker than anticipated.
- Insufficient amounts of reinforcing steel, causing Thermal Cracking due to heating on the outside and cool water on the inside
our media
Explore Our other Informational Resources
Gallery
Visuals showcasing our projects and equipment in action.
Information for you
Aqua Facts
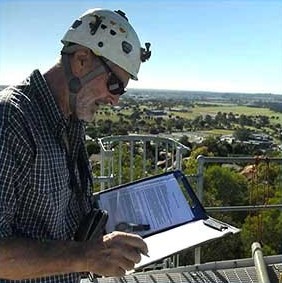
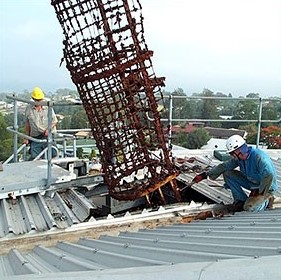
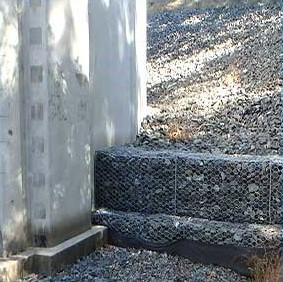
Information for you
Aqua Facts
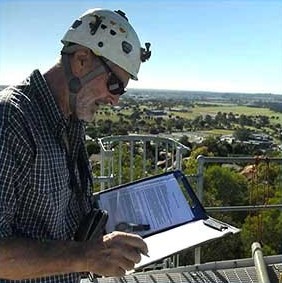
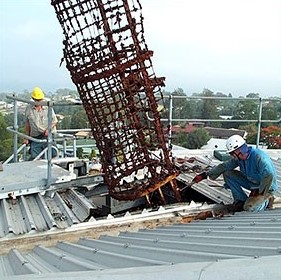
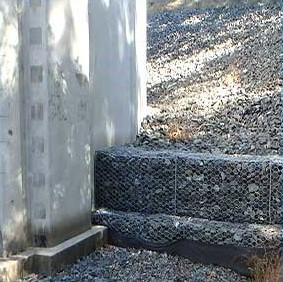